It usually costs between $1 and $15 to recycle each kilogram of an electric car battery. So, the total recycling cost for a typical 500-kilogram battery can be anywhere from $500 to $7,500. Pyrometallurgy ($5-$10/kg) is more energy-intensive but widely used, while hydrometallurgy ($10-$15/kg) is more environmentally friendly but costlier. According to the latest industry forecasts, the recycling market is projected to grow from $3.5 billion in 2024 to over $23.7 billion by 2035. This comprehensive guide covers all aspects of EV battery recycling costs, including processes, challenges, and future trends.
Expert Insight: “The economics of battery recycling are rapidly improving. What cost $15/kg in 2020 can now be done for as little as $7/kg with advanced techniques, and we expect costs to decrease another 30% by 2030 as scale increases.”
Dr. Linda Gaines, Argonne National Laboratory
Understand EV Battery Recycling Costs In 2025
EV battery recycling is a multi-step process involving collection, transportation, disassembly, material separation, and refinement. The total cost of recycling comes from the price of each individual part of the process.
Current Cost Breakdown (2025 Data)
Process Stage | Cost Range (per kg) | Percentage of Total Cost |
---|---|---|
Collection & Transportation | $0.20-$2.00 | 15-20% |
Disassembly & Sorting | $0.30-$3.00 | 20-25% |
Material Processing | $0.50-$10.00 | 50-60% |
Environmental Compliance | $0.10-$1.00 | 5-10% |
A recent study by MarketsandMarkets 2025 predicts that the worldwide market for recycling electric car batteries will grow by an average of 40.9% each year from 2024 to 2035. By 2035, this market is expected to reach $23.72 billion. Because more and more people are choosing electric cars and because regulations are pushing for responsible battery disposal, the battery recycling market is seeing huge growth.
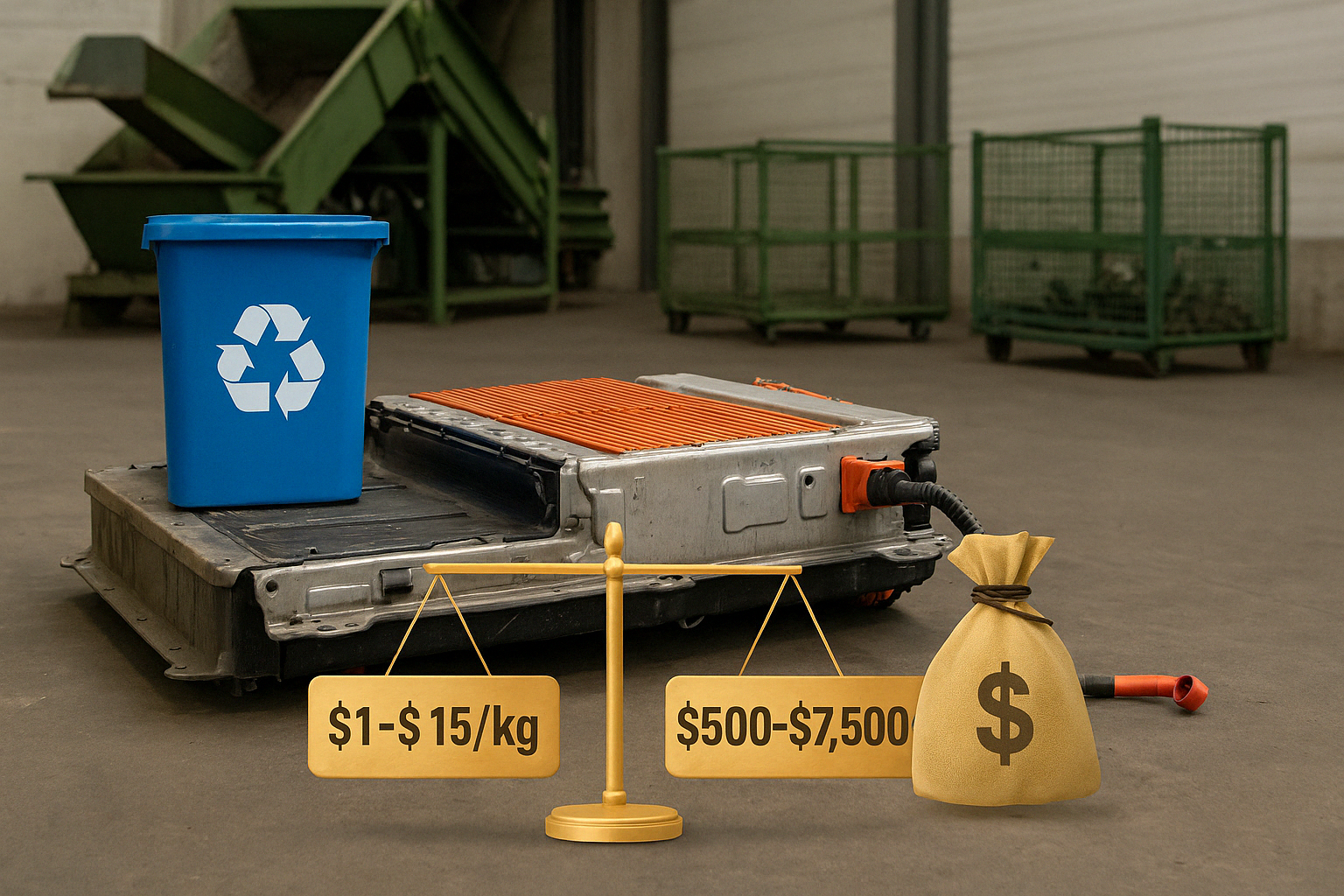
Major Recycling Methods Compared
1. Pyrometallurgy
Pyrometallurgy uses high temperatures (typically 1400-1700°C) to break down battery components and extract valuable metals like lithium, nickel, and cobalt.
Pros: – Effective for mixed battery chemistries – High recovery rates for cobalt and nickel (95 %+) – Established technology with proven scalability.
Cons: – Energy-intensive (3-5 MWh per ton of batteries) – Higher carbon footprint (1.8-2.2 tons CO₂ per ton processed) – Lower recovery rates for lithium (30-50%) – Costs $5-$10 per kilogram.
Real-world example: Umicore’s facility in Belgium processes 7,000 tons of batteries annually using pyrometallurgy, recovering over 95% of cobalt and nickel with a carbon footprint of approximately 1.9 tons CO₂ per ton processed.
2. Hydrometallurgy
Hydrometallurgy uses chemical solutions to extract metals through leaching, precipitation, and electrowinning processes.
Pros: – Higher recovery rates for lithium (80-95%) – Lower energy consumption (0.8-1.5 MWh per ton) – Reduced emissions (0.5-0.9 tons CO₂ per ton) – More selective material recovery.
Cons: – More complex process requiring specialized equipment – Higher chemical usage and wastewater management needs – Higher capital investment requirements – Costs $10-$15 per kilogram.
Example: Li-Cycle’s hub-and-spoke model uses hydrometallurgy to achieve up to 95% material recovery rates and approximately 60% lower carbon emissions than pyrometallurgy.
3. Direct Recycling (Emerging Technology)
Direct recycling aims to recover cathode materials without breaking down their chemical structure, preserving more value.
Pros: Potential for lowest cost ($3-$6 per kilogram when scaled), Highest material value retention, Lowest energy requirements (0.5-0.8 MWh per ton), and minimal chemical usage.
Cons: – Still in development/early commercialisation – Works best with sorted, single chemistry batteries – Limited commercial-scale facilities – Currently higher costs due to low scale ($12-$20 per kilogram).
Research breakthrough: Argonne National Laboratory’s direct recycling process demonstrated 93% cathode material recovery with 88% of original performance in 2024 tests, potentially reducing recycling costs by up to 40% when commercialised.
Extracting Black Mass
“Black mass” is a mix of materials like carbon, nickel, manganese, and cobalt oxides found in electric car batteries. It makes up about 60% of the battery’s weight and is one of the most valuable things we can get back when we recycle them.
Current Market Values (May 2025)
Material | Value per Metric Ton | Typical Recovery Rate | Net Value per Battery |
---|---|---|---|
Black Mass | $300-$500 | 90-95% | $90-$285 |
Copper | $450-$500 | 85-95% | $38-$48 |
Aluminum | $50-$60 | 90-98% | $5-$6 |
Lithium | $15,000-$18,000 | 30-90%* | $45-$162 |
Cobalt | $35,000-$40,000 | 85-98% | $298-$392 |
Nickel | $18,000-$22,000 | 90-97% | $162-$213 |
Source: London Metal Exchange prices, May 2025, and industry recovery benchmarks
EV Battery Recycling Cost Estimator Tool
Key Factors Affecting EV Battery Recycling Costs
Several factors influence the cost of recycling EV batteries. Understanding these factors helps in assessing the overall expense.
1. Battery Chemistry And Design
Different battery chemistries require specific recycling approaches, directly impacting costs:
- NMC (Nickel Manganese Cobalt): Higher value recovery due to cobalt content, typically $8-$12/kg to recycle.
- LFP (Lithium Iron Phosphate): Lower material value but simpler process, typically $5-$8/kg to recycle.
- NCA (Nickel Cobalt Aluminum): Similar to NMC in recycling costs, typically $7-$11/kg to recycle.
- Solid-state batteries: Emerging technology with potentially lower recycling costs due to reduced hazardous materials.
Design impact: Tesla's structural battery pack design increases disassembly costs by approximately 15-20% compared to modular designs, according to a 2024 study by the National Renewable Energy Laboratory.
2. Collection and Transportation
The logistics of gathering and transporting end-of-life batteries represent a significant cost factor:
- Transportation costs: $0.15-$0.40 per kg per 100 miles.
- Hazardous material handling: Adds 20-30% to base transportation costs.
- Regional variations: EU transportation costs average 15-25% higher than the US due to regulatory requirements.
Cost-saving innovation: Battery Resourcers developed specialized EV battery transport containers in 2024 that reduce shipping costs by up to 35% while improving safety compliance.
3. Scale of Operations
Economies of scale significantly impact per-unit recycling costs:
- Small facilities (<1,000 tons/year): $10-$15 per kg.
- Medium facilities (1,000-10,000 tons/year): $5-$10 per kg.
- Large facilities (>10,000 tons/year): $1-$5 per kg.
Industry example: Redwood Materials' Nevada facility processes over 20,000 tons annually and achieves recycling costs below $3 per kg for specific battery types due to operational scale and integrated processing.
4. Regulatory Compliance
Following the rules for environmental protection and safety makes recycling more expensive:
- EU Battery Directive: For example, the European Union's rule states that 70% of a battery's materials must be recovered by 2030. This adds about $0.50 to $1.00 to the cost of recycling each kilogram of battery.
- US EPA requirements: Hazardous waste handling adds $0.30-$0.80/kg.
- China's recycling standards: Mandate 98% recovery efficiency for certain materials, adding $0.40-$0.90/kg.
Compliance strategy: Leading recyclers like Li-Cycle have invested in advanced emissions control systems that exceed regulatory requirements, reducing long-term compliance costs by 25-30%.
Challenges in Reducing EV Battery Recycling Costs
Several challenges hinder cost reduction in EV battery recycling.
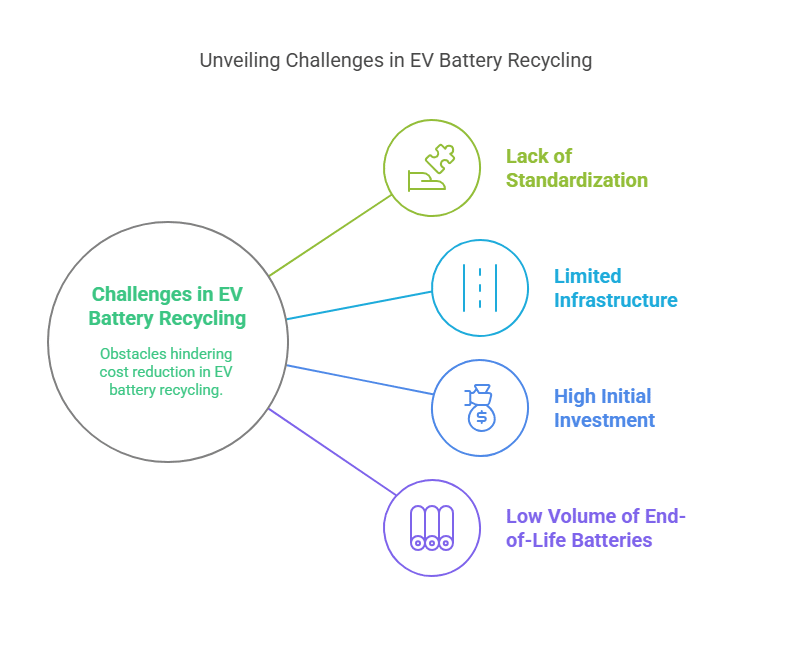
1. Lack of Standardization
The fact that batteries are designed in many ways and use different chemicals creates difficulties for recycling.
- Over 20 different EV battery designs are currently in production.
- Disassembly procedures vary significantly between manufacturers.
- Automated disassembly systems must be reprogrammed for different designs.
The Global Battery Alliance's Battery Passport program, launched in 2024, aims to standardize battery design information to improve recycling efficiency, potentially reducing costs by 15-20%.
2. Limited Infrastructure
The recycling ecosystem is still developing:
- Only 25-30 commercial-scale EV battery recycling facilities exist globally.
- Current global capacity can process only about 30% of the available end-of-life batteries.
- Regional imbalances leave some areas with minimal recycling options.
Investment trend: PitchBook's data shows a strong investment trend in battery recycling. In 2024, $3.2 billion was invested in the necessary facilities, a 65% rise from 2023, signaling a quick increase in the amount we can recycle.
3. High Initial Investment
Building recycling facilities requires significant capital:
- Small facility (1,000 tons/year): $20-$30 million investment.
- Medium facility (5,000 tons/year): $50-$100 million investment.
- Large facility (10,000+ tons/year): $ 100- $ 300+ million investment.
Green bonds specifically for battery recycling infrastructure raised over $1.5 billion in 2024, reducing capital costs by approximately 1.5-2.5% compared to traditional financing.
4. Low Volume of End-of-Life Batteries
Most EVs sold in the last decade are still in operation:
- Only 5-8% of EV batteries reached end-of-life in 2024.
- Volume expected to increase 300% by 2030.
- Current "chicken and egg" problem: low volume → high costs → limited investment.
Volume projection: According to the International Energy Agency (2025), the supply of EV batteries for recycling will reach approximately 1.2 million metric tons by 2030, up from 180,000 metric tons in 2025.
The Future of EV Battery Recycling Costs
The future looks promising for EV battery recycling. Several trends could reduce costs over time.
1. Technological Advancements
New recycling technologies are developing rapidly. These techniques aim to improve effectiveness and reduce expenses. Direct component recycling offers a promising solution to boost economic performance.
2. Increased Scale
As most electric vehicles (EVs) end their usable lives, people will recycle more of these cars. When recycling centres process more gel battery units, they can achieve cost savings due to increased efficiency. The increased efficiency will then lower the general expenses associated with recycling.
3. Government Support
Governments increasingly understand that battery recycling significantly impacts sustainability. Many governments offer financial support and subsidies, which lead to improved battery recycling technology.
4. Industry Collaboration
Car companies and battery recyclers must create a shared plan. They need a plan for battery design and recycling. A typical plan will make the processes easier, improve efficiency, and reduce the cost of operations.
5. Rising Material Prices
Lithium and cobalt nickel prices are set to increase in the future. More expensive material translates to more profitability associated with the recycling process, which opens doors to a broader range of companies.
Environmental and Economic Benefits
Recycling EV batteries offers both environmental and economic benefits.
1. Resource Conservation
Recycling helps reclaim necessary materials. When these resources are recovered, the necessity for mining is lessened. Mining harms the environment. As a result, recycling preserves important natural resources.
2. Pollution Reduction
Recycling waste helps prevent harmful substances from entering landfills. Utilizing materials recovered through recycling keeps the air and water clean from contaminants.
3. Job Creation
Many people are employed in the recycling sector. Recycling helps local communities create new jobs. Gathering, moving, and processing resources all provide jobs. These positions lower unemployment and strengthen the local economy.
4. Cost Savings
Recycling can lower the cost of producing new batteries. Recovered materials are cheaper than newly mined ones. This can reduce the overall cost of EVs.
Practical Considerations For EV Owners And Stakeholders
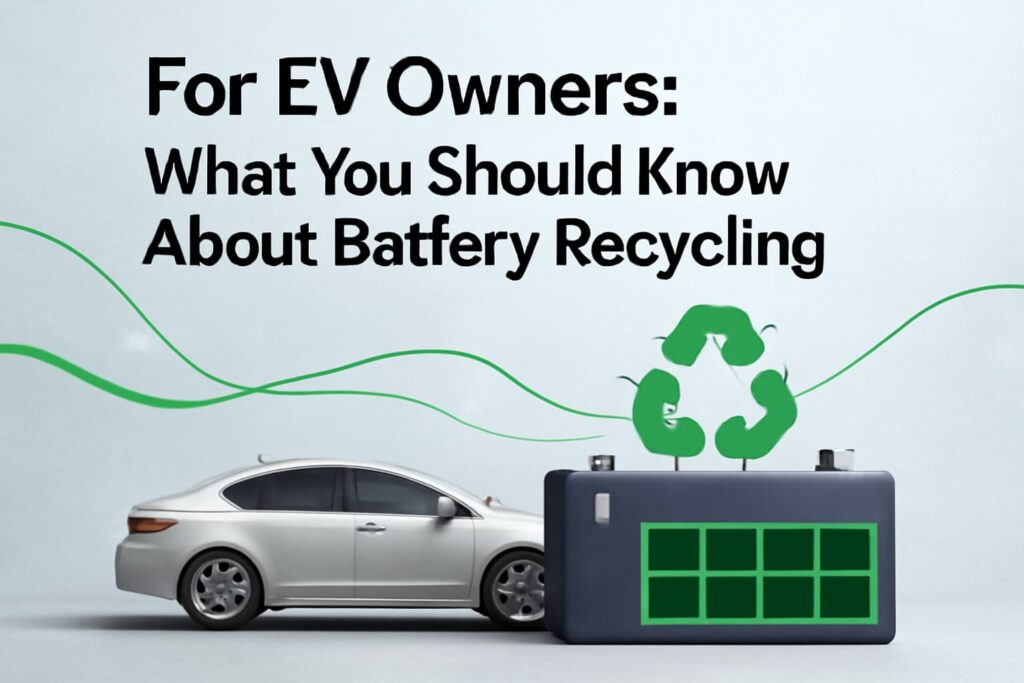
For EV Owners
If you own an electric vehicle, here's what you should know about battery recycling:
- Battery lifespan: Most EV batteries last 8-15 years or 100,000-200,000 miles.
- End-of-life options: Return to manufacturer, sell to recycler, or repurpose for energy storage.
- Potential value: A used but functional EV battery can be worth $1,500-$5,000, depending on condition.
- Disposal regulations: Improper disposal can result in fines of $10,000+ in many jurisdictions.
Owner tip: Many manufacturers now offer battery buy-back programs that can provide a $500-$2,000 credit toward a new vehicle purchase when returning an end-of-life battery.
For Fleet Operators
Organizations managing EV fleets should consider:
- Battery health monitoring: Predictive analytics can extend battery life by 15-25%.
- End-of-life planning: Establish recycling contracts before batteries reach end-of-life.
- Volume advantages: Negotiating recycling for multiple batteries can reduce per-unit costs by 20-30%.
- Regulatory compliance: Maintain proper documentation of battery disposal.
Fleet strategy: Amazon's fleet management program, implemented in 2024, reduced battery replacement costs by 18% through predictive maintenance and secured favorable recycling terms through volume commitments.
For Recycling Entrepreneurs
Those considering entering the recycling business should evaluate:
- Minimum viable scale: 500-1,000 tons/year, typically needed for profitability.
- Technology selection: Match process to available battery chemistry mix.
- Regulatory landscape: Permits can take 12-18 months to secure.
- Partnership opportunities: Collaborations with manufacturers can secure feedstock.
Business model insight: Successful recycling startups in 2024-2025 have focused on regional processing hubs that minimize transportation costs while achieving sufficient scale for profitability.
In Short
EV battery recycling costs range from $1 to $15 per kilogram, depending on the method, scale, and location. Pyrometallurgy ($5-$10/kg) is more energy-intensive but widely used, while hydrometallurgy ($10-$15/kg) offers environmental advantages at a higher cost.
The industry is rapidly evolving, with costs projected to decrease by 40-60% by 2030 due to technological improvements, increased scale, and supportive policies. As material prices rise and environmental regulations tighten, recycling will become increasingly economical and necessary.
If you're considering recycling methods, hydrometallurgy might be worth the higher cost for its environmental benefits, especially as technology improves and these costs become more manageable.
Read more about EV Battery Recycling.
FAQs
What factors influence the cost of recycling EV batteries?
Key factors include battery chemistry, transportation logistics, recycling technology (e.g., pyrometallurgy vs. hydrometallurgy), operational scale, regulatory compliance, and fluctuating market prices of recovered materials like lithium and cobalt.
How much does it cost to recycle a single EV battery?
Recycling costs range from 1 to 15 per kilogram. Depending on the method and location, the total cost for a typical 500 kg EV battery can vary between 500 and 7,500.
What challenges make EV battery recycling cost?
1. Lack of standardized battery designs.
2. Limited recycling infrastructure and high upfront facility costs.
3. Low volume of end-of-life batteries (most EVs are still new).
4. Complex disassembly requirements.
5. Stringent environmental regulations.
How could future trends reduce recycling costs?
1. Technological advancements in automated disassembly and direct recycling.
2. Increased processing volume as more EVs reach end-of-life.
3. Government incentives and supportive policies.
4. Industry collaboration between automakers and recyclers.
5. Rising prices of battery materials are improving recycling economics.
Is Battery Recycling Profitable In 2025?
Profitability varies by operation scale and material prices. Large-scale operations (>10,000 tons/year) using advanced processes can achieve 15-25% profit margins, while smaller operations may struggle to break even. The industry is projected to become increasingly profitable as technology improves and material prices rise.
How Do Different Recycling Methods Compare In Cost?
Pyrometallurgy: $5-$10 per kilogram, energy-intensive but effective for mixed
batteries.
Hydrometallurgy: $10-$15 per kilogram, more environmentally friendly with
Higher recovery rates.
Direct recycling: Currently, it costs $12-$20 per kilogram, but it could potentially drop to $3-$6 when scaled, preserving more material value.
What Percentage Of An EV Battery Can Be Recycled?
Modern recycling processes can recover 70-95% of battery materials by weight. Recovery rates vary by material: 95-98% for cobalt and nickel, 90-98% for aluminum and copper, and 30-95% for lithium (depending on the recycling method used).
Note: Our team originally wrote this article and later enhanced it using AI assistance, with thorough human review and fact-checking to maintain accuracy and quality.